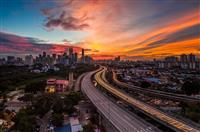
钻机循环系统
钻机循环系统是指将钻井液循环到钻头再将其返回地面进行清洁和再循环的设备。对旋转钻井系统来说,循环系统的功能就是通过钻柱将钻井流体向下循环到钻头,通过钻头沿钻柱和井壁或套管内壁形成环空向上循环。循环系统主要由钻井泵、水龙带、水龙头或顶驱、钻柱、钻头、钻井液回流管线、固相控制设备、泥浆罐(池)等组成。
本篇主要介绍钻井泵、钻井液净化系统的基本组成和原理。
第一部分
钻井泵
钻井泵在石油矿场上应用非常广泛,常用于高压下输送高黏度、高密度和高含砂量、高腐 蚀性的液体,流量相对较小。按用途的不同,石油矿场用钻井泵往往被冠以相应的名称,例如在钻井过程中,为了携带出井底的岩屑和供给井底动力钻具的动力,用于向井底输送和循环钻 井液的钻井泵称为钻井泵;为了固化井壁,用于向井底注入高压水钻井液的钻井泵,称为固井泵;为了造成油层的人工裂缝,提高原油产量和采收率,用于向井内注入含有大量固体颗粒的液体或酸碱液体的钻井泵,称为压裂泵;用于向井内油层注入高压水驱油的往复泵,称为注水泵;在采油过程中,用于在井内抽汲原油的钻井泵,称为抽油泵。
石油工业的发展对往复泵提出更高的要求,如泵压要高,功率要大,而制造和维修成本要低,体积和重量不能过大。由于石油矿场用钻井泵的工作条件十分恶劣,提高其易损件(如泵阀、活塞一缸套副、柱塞一密封副等)的工作寿命便成为往复泵设计、制造和使用中迫切需要解决的问题。
一
钻井泵的工作原理
图3-1 钻井泵工作示意图
1一曲柄;2一连杆;3一十字头;4一活塞;5一缸套;6—排出阀;7—排出四通;8-预压排出空气包;9—排出管;10—阀箱(液缸);11一吸入阀;12—吸入管
如图3-1所示,卧式单缸单作用往复式钻井泵。主要由液缸、活塞、吸入阀、排出阀、阀室、曲柄或曲轴、连杆、十字头、活塞杆以及齿轮、皮带轮和传动轴等零部件组成。当动力机通过皮带、齿轮等传动件带动曲轴或曲柄按图示方向,从左边水平位置开始旋转时,活塞向右边即泵的动力端移动,液缸内形成一定的真空度,吸入池中的液体在液面压力的作用下,推开吸入阀,进入液缸,直到活塞移到右死点为止,此为液缸的吸入过程。曲柄继续转动,活塞开始向左边即液力端移动,液缸内液体受挤压,压力升高,吸人阀关闭,排出阀被推开,液体经排出阀和排出管进入排出池,直到活塞移到左死点为止,此为液缸的排出过程。曲柄连续旋转,每一周内活塞往复运动一次,单作用泵的液缸完成一次吸入和排出过程。
在吸入或排出过程中,活塞移动的距离以S表示,称作活塞的冲程长度,曲柄半径用r表示,它们之间的关系为S=2r。
钻井泵的基本性能参数有以下6个∶
(1)泵的理论排量∶泵在单位时间内排出的介质体积称为泵的理论平均排量,简称为泵的理论排量。
(2)泵的工作压力∶通常是指泵排出口处单位面积上所受到的液体作用力,简称为泵压。
(3)泵的功率∶单位时间内动力机传递给泵主动轴的能量,称为泵的输入功率;泵工作于额定冲次时的输入功率称为泵的额定功率;单位时间内液体经泵作用后增加的能量称为有效功率,也称为水功率。
(4)泵的效率∶是指有效功率与输人功率的比值。
(5)冲次∶也称泵冲,指单位时间内活塞的往复次数。
(6)冲程长度∶指活塞往复运动的距离。
二
钻井泵的分类
按照结构特点,石油矿场用钻井泵大致可以按以下几个方面分类∶
(1)按缸数分有单缸泵、双缸泵、三缸泵、四缸泵等。
(2)按直接与工作液体接触的工作机构分有活塞式及柱塞式两种。
(3)按作用方式分主要有单作用式和双作用式两种。
①单作用式泵的活塞或柱塞在液缸中往复一次,该液缸作一次吸人和一次排出;
②双作用式泵的液缸被活塞或柱塞分为两个工作室,无活塞杆的为前工作室或称前缸,有活塞杆的为后工作室或称后缸,每个工作室都有吸入阀和排出阀,活塞往复一次,液缸吸入和排出各两次。
(4)按液缸的布置方案及其相互位置分有卧式泵、立式泵、V形或星形泵等。
(5)按传动或驱动方式分常见的有∶
①机械传动泵,如曲柄一连杆传动、凸轮传动、摇杆传动、钢丝绳传动往复泵及隔膜泵等;
②蒸汽驱动钻井泵;
③液压驱动钻井泵等,近几年来,液压驱动往复泵在油田越来越受到重视。
石油矿场用钻井泵广泛应用三缸单作用和双缸双作用卧式活塞泵;压裂、固井及注水泵常用三缸、五缸单作用卧式柱塞泵及其他类型的往复泵。
三
钻井泵的型号代码及其技术规范
用于石油和天然气钻井的国产泵已实现了标准化,目前所用的钻井泵都是三缸单作用卧式活塞泵,其中NB表示钻井泵,NB前面的数字表示泵的液缸数,无数字为双液缸,NB的下标表示设计序号,后面的数字表示泵的额定输入功率(马力),型号代码如图3-2所示。
图3-2国产钻井泵的型号代码示意图
宝鸡石油机械有限责任公司制造钻井泵的型号代码如图3-3所示。
图3-3宝石产钻井泵的型号代码示意图
国外的钻井泵一般具有不同的代号,多数按制造厂家编排的系列而定,但代号后面或前面的一组数字,通常表示该泵的额定输人功率(马力)或1/10倍数。常用国产钻井技术规范参数见表3-1。
表3-1常用国产钻井泵技术规范
四
三缸单作用钻井泵的组成
三缸单作用钻井泵由动力端和液力端两大部分组成,如图3-4所示。
图3-4 3NB-1300 三缸单作用活塞泵主剖面图
1—泵体;2—机座;3一动力端总成;4一缸套;5—活塞;6—吸入阀;7-排出阀;8—起重架
1.动力端
三缸单作用活塞泵的动力端主要由主动轴(传动轴)、被动轴(主轴或曲轴)、十字头等组成。
1) 传动轴总成
通常三缸单作用活塞泵传动轴的两端对称外伸,可以在任意一端安装大皮带轮或链轮。两端的支承采用双列向心球面球轴承或单列向心短圆柱滚子轴承,保证可以有一定的轴向浮动。
2) 曲轴总成
曲轴是钻井泵中最重要的零件之一,其结构和受力都十分复杂,其上安装有大人字形齿轮和三根连杆大头,大齿轮圈通过螺栓与曲轴上的轮毂紧固为一体。三个连杆轴承的内圈热套 在曲轴上,连杆大头热套在轴承的外圈上。
3)十字头总成
十字头是传递活塞力的重要部件,同时,又对活塞在缸套内作往复直线运动起导向作用, 使介杆、活塞等不受曲柄切向力的影响,减少介杆和活塞的磨损。曲轴通过连杆和十字头销带 动十字头体,十字头体又通过介杆带动活塞。曲柄和十字头的结构位置可参看图3-1。
2.液力端
三缸单作用泵的每个缸套只有一个吸入阀和排出阀,故其液力端结构比双作用泵液力端简单得多。目前的三缸单作用泵泵头主要有L形、I形和T形三种形式。
1)L形泵头
图3-5所示为L形泵头的示意图。L形泵头可将吸入泵头和排出泵头分块制造。其优点是吸入阀可以单独拆卸,检修和维护方便,钻井液漏失较少;缺点是结构不紧凑,泵内余隙流道长,泵头质量大,自吸能力较差。
图3-5 L形泵头
1一吸入管汇;2一吸人阀;3一活塞;4一活塞杆;5—排出阀;6—排出管汇
2)I形泵头
图3-6所示为I形泵头的示意图。这种直通形泵头的液力端结构紧凑,重量较轻,缸内余隙流道长度短,有利于自吸;但更换吸人阀座时,必须先拆除上方的排出阀;采用带筋阀座时,还要先取出排出阀座,检修比较困难。
3)T形泵头
T形泵头主要特点是吸入阀水平布置,排出阀垂直布置,综合了L形和I形泵头的优点,既可分块制造,便于吸入阀的拆装和检修,又取消了吸人室,使泵头结构紧凑,内部余隙容积减小,质量减小。T形泵头不足之处是更换吸入阀时需卸下吸人液缸及弯管,钻井液漏失相对多一些。
五
钻井泵的安全保护装置
为了保证钻井泵输出液体的压力平稳,在钻井液出口端要安装空气包;为了在倒换阀门出错、钻头泥包或者水眼被堵的情况下高压钻井液有个安全出口,在钻井泵的出口端需要安装安全阀。空气包和安全阀如图3-7所示。
图3-7 空气包和安全阀
1一空气包;2一压力表;3一剪销安全阀;4一钢圈;5一法兰螺栓;6—排出四通;7一垫环;8—螺母NPT,ZC一丝扣型号
1.空气包
空气包的作用是减小因钻井泵瞬时排量变化而产生的压力波动,使泵压平稳,使设备不 致因剧烈震动而造成损坏。空气包胶囊内要求充氮气或惰性气体,在没有氮气或惰性气体的情况下可用空气代替,严禁充入氧气或可燃性气体。充气压力为最高工作压力的20%~30%。
钻井泵活塞处于排出过程时,排出管内流体流速加快,压力也随之升高,当压力大于空气包气室内的压力时,气囊被压缩,部分液体进入空气包;当活塞处于吸入过程、排出管内液体压 力小于空气包气室的压力时,气囊开始膨胀,挤出空气包内的液体。随着排出和吸入过程的不断重复进行,空气包不断交替地储存和排出液体,自动调节排出管中的流体速度和压力,达到稳定泵压的目的。
目前使用最广泛的是球形隔膜式预压空气包,它是一个内充空气(一般为氮气)的密闭容器,主要由壳体和橡胶囊组成,胶囊上口被固定在壳体上。工作时随排出或吸入的变化,胶囊底部上下运动,以储存或挤出液体。钻井泵排出阀附近都安装有空气包(排出空气包),有时也在吸入阀附近安装空气包(吸入空气包)。
2.安全阀
往复泵一般都在高压下工作,为了保证安全,在排出口处安装有安全装置,即安全阀,以便将泵的极限压力控制在允许的范围内。常见的安全阀为销钉剪切式,此外,还有膜片式和弹簧式等安全阀。活塞或膜片下端有高压液体,当压力达到一定值后,活塞推动连杆,切断销钉,活塞上移或膜片破裂,髙压液体由安全阀排出口进入吸入罐或大气空间,达到泄压以保证安全的目的。
杠杆剪切式安全阀只需要同一种材料和同一种截面的销钉,对于不同压力的规定值,改变安全阀销钉的位置即可,销钉距离力的作用点越远,承受的压力就越高。
直接销钉剪切式安全阀结构简单,拆卸容易,但安全销钉的材料、尺寸及加工工艺必须恰当,还要防止安全阀的活塞和导杆在缸套内锈蚀,否则灵敏度将会降低,不能准确地控制排出压力。
第二部分
钻井液净化系统
清除钻井液中固相含量的过程,称为钻井液的净化。实践证明,钻井液净化是非常必要的,这是因为若钻井液中固相含量过多,将产生不良后果(如降低钻井液携带岩屑的能力和钻头的工作效率;使钻井液密度和黏度不必要地上升;钻井液中过多的颗粒会加速整个钻井液循环系统机械设备的磨损,影响设备寿命,增加维修工作量)。
清除钻井液中的固相一般分为物理方法和化学方法,物理方法就是通过振动筛、除砂器、除泥器、离心机等机械设备,利用筛分、离心分离等原理,将钻井液中的固相按密度和颗粒大小的不同而分离,根据需要而取舍,以达到控制固相的目的。
一
钻井液净化系统的净化分级
钻井液净化系统主要由一组储存钻井液的固控罐及用于清除钻井液中有害固相的设备组成,罐面上安装有振动筛、除砂器、除泥器、离心机等用于净化钻井液的设备。该系统主要由五级净化组成∶
(1)一级净化,即钻井液在振动筛的处理。配制好的钻井液在钻井泵的作用下进入井底,并携带钻进岩屑返回地面,经过井口高架管进入振动筛,将钻井液中较大的岩屑筛分出来。
(2)二级净化,当钻井液有气侵时,可通过真空除气器将钻井液中的气体清除,从而恢复钻井液密度、稳定钻井液黏度。
(3)三级净化,二级净化后的钻井液经除砂器供液泵进入除砂器,钻井液中40~60μm以上的细小有害固相在除砂器里被分离出来。
(4)四级净化,三级净化后的钻井液经除泥器供液泵进入除泥器,钻井液中15~40μm以上的细小有害固相在除泥器里被分离出来。
(5)五级净化,四级净化后的钻井液经离心机供液泵进入离心机,离心机将钻井液中5~15μm微小的颗粒分离出来。
通常这五级净化是同时进行的。如果只进行其中一项或几项净化,钻井液参数就能满足作业要求时,可以只进行这一项或这几项净化。钻井液的净化过程完成后,钻井液即可进入下一个正常的钻井循环。
近年来,不少钻机已将全套净化装置组成一个整体封闭式系统,装在一个带橇座的大罐上,由于设备先进、齐全,泵、管线、罐等与各设备之间的相对位置布置合理,可将钻井液中的钻屑全部清除,水耗仅为常规净化系统的10%,钻屑几乎可以干粒状排出,既可节约钻井费用,又能防止对环境的污染。整体封闭式系统流程如图3-8所示。
图3-8整体封闭式净化系统流程图
1—井口返出钻井液;2—振动筛;3—除气器;4—钻井液清洁器;5—稀释;6—进浆;7—标准离心机;8—重晶石;9—储罐;10—高速离心机;11—废弃固相;12—吸人罐。
二
固控系统的配置
为了满足钻井工况对钻井液质与量的需要,不同型号的钻机在固控系统配备上(固控罐的容积、设备配置、流程布置等)有所区别。
根据SY/T6223—2005《钻井净化设备配套、安装、使用和维护》中的内容,4000~7000m 钻机的钻井液净化装置主要性能参数及设备配置见表3-2、表3-3、表3-4。
表3-2 4000m钻机钻井液净化系统的配套
表3-3 5000m钻机钻井液净化系统的配套
表3-4 7000m钻机钻井液净化系统的配套
三
振动筛
振动筛是固控系统中最重要的净化设备,作为钻井液的第一级净化,其作用是将从井口返出的钻井液中大于70μm的较大颗粒除去,并且不产生破碎,以便下一级净化设备对钻井液进一步净化。振动筛性能的优劣除直接影响第一级处理的质量,对下级净化处理设备性能的发挥也有很大的影响。
图3-9钻井液振动筛
1——钻井液进口;2—钻井液盒;3—筛网;4一筛除粗固相颗粒;5—底座;6—隔振元件;7—筛箱;8一液体和细固相颗粒
石油矿场中使用的多为单轴惯性振动筛,主要由筛箱、筛网、隔振弹簧及激振器等组成,其示意图如图3-9所示。由主轴、轴承和偏心块等构成的激振器,旋转时产生周期性的惯性力,迫使筛箱、筛网、弹簧等部件在底座上作简谐振动或准简谐振动,促使由钻井液盒均匀流到筛网表面的钻井液固相分离,即液体和较小颗粒通过筛网孔流向除砂器,而较大颗粒沿筛网表面移向砂槽。
钻井液振动筛中最易损坏的零件是筛网。一般有钢丝筛网、塑料筛网、带孔筛板等,常用的是不锈钢丝的筛网。筛网通常以"目"表示其规格,"目"表示以任何一根钢丝的中心为起点,沿直线方向25.4mm(lin)上的筛网数目。例如某方形孔筛网每英寸有12孔,称作12目筛网,用API标准表示为12×12。对于矩形孔筛网,一般也以单位长度(in)上的孔数表示,如80 ×40表示 lin 长度的筛网上,一边有80孔,另一边为40孔。
常用振动筛性能参数见表3-5。
表3-5常用振动筛的主要性能参数
四
除砂器、除泥器
实践证明振动筛一般只能清除25%左右的固相量,74μm以下的细微颗粒仍然留在钻井液中,对钻进速度仍然影响很大。为了进一步改善钻井液性能,一般在钻井液振动筛之后装有水力旋流器,用以清除较小颗粒的固相。水力旋流器分为除砂器和除泥器两种,二者的结构和工作原理完全相同。除砂器的锥筒内径一般为6~12in,能清除大于70um和约50%的大于45μm的细砂颗粒。除泥器的锥筒内径一般为2~5in,能清除大于40μm和约50%大于15um 的泥质颗粒(锥筒内径是指锥筒圆柱体部分的内径,也称为工作内径)。
除砂器、除泥器在固控系统中为第二、第三级净化设备,是由进液管、排液管、旋流器、清洁筛、底座、支架及其他部件构成,如图3-10所示。
图3-10 除砂器、除泥器
1—电动机;2一底座;3—支架;4—旋流器;5—排砂槽;6—清洁筛
1.旋流器的结构及工作原理
水力旋流器的结构原理如图3-11所示,其上部呈圆筒形,形成进口腔,侧部有一切向进口管,由砂泵输送来的钻井液沿切线方向进入腔内。顶部中心有涡流导管,处理后的钻井液由此溢出。壳体下部呈圆锥形,锥角一般为150°~200°,底部为排砂口,排出固相。
图3-11水力旋流器
水力旋流器与一般分离机械不同,它没有运动部件,是利用钻井液中固、液相各颗粒所受的离心力大小不同进行分离。切向进入的具有一定压力的钻井液,在旋流器内腔旋转时产生离心力,质量较大的固相颗粒受到较大的离心力,其足以克服钻井液的摩擦阻力,被甩到旋流器的内壁上,并靠重力作用向下旋流,由排砂口排出;而质量小的固相颗粒及轻质钻井液则螺旋上升,经溢流管输出。
2.旋流器的分类
旋流器上部壳体圆筒部分的直径是决定旋流器钻井液处理量及分离钻井液中泥砂颗粒大小的重要因素,圆筒部分的直径称为旋流器的名义尺寸。下部壳体的圆锥角一般在15°~20°之间,底流口直径在10~30mm 之间。一般情况下由一组名义尺寸在150~300mm 之间的旋流器组成的净化设备称之为除砂器,由一组名义尺寸在50~125mm之间的旋流器组成的净化设备称之为除泥器。
1)除砂器
根据除砂器对钻井液处理量的大小,一般情况下除砂器由1~3个150~300mm的旋流器组成。每个旋流器的处理能力,在进液压力为0.2MPa 时不低于 20~120m²/h。正常工作的除砂器能清除约95%大于74μm的岩屑和约50%大于40μm的岩屑。为了提高使用效率,在选用除砂器时其许可处理量必须为钻井时最大排量的125%。
2)除泥器
根据除泥器对钻井液处理量的大小,一般情况下除泥器由4个以上50~125mm的旋流器组成。每个旋流器的处理能力,在进液压力为0.2MPa时不低于5~15m²/h。正常工作的除泥器能清除约95%大于40μm的岩屑和约50%大于15μm的岩屑。除泥器能除去12~13μm 的重晶石,因此不能用它来处理加重钻井液。在选用除泥器时,其许可处理量必须为钻井时最大排量的125%~150%。
3)清洁器
清洁器是旋流器与超细网振动筛的组合,上部为旋流器,下部为超细网振动筛。清洁器是二次处理设备。它处理钻井液的过程分两步∶第一步是旋流器把钻井液分离成低密度的溢流和高密度的底流;第二步是超细网振动筛将高密度的底流分成两部分,一部分是重晶石和其他小于网孔的颗粒,它们透过筛网,另一部分是大于网孔的颗粒它们从筛网尾部排出。常用旋流器的规格及工作参数见表3-6。
表3-6常用旋流器的规格及工作参数
3.旋流器使用注意事项
目前,现场使用的水力旋流器多属于惯性型。另外,还有一种高效水力旋流器,如图3-12所示。它的独特之处是有三根溢流管,当钻井液进入时,重而大的固相颗粒被甩向筒壁,并螺旋下降,经排砂口排出;而轻质部分则从各溢流管溢出,不再形成螺旋上升的轻质液柱,消除了空气柱,减少了内部的水力损失,从而提高了钻井液处理量及液体的净化程度。
图3-12 高效能水力旋流器
1一锥体;2—进液管;3—压盖;4,5,6—溢流管;7—短圆筒;8—底流口
水力旋流器分离出固相颗粒的粒径越小,则分离能力越大,它与旋流器的尺寸、进浆压力、钻井液黏度及固相颗粒的分布等有关。由于钻井液中固相颗粒高速撞击旋流器内壁,并沿内壁快速旋转下落,往往导致旋流器内壁很快磨损、破坏。常用钻井液除砂器、除泥器性能参数见表3-7。
表3-7钻井液清洁器主要性能参数
五
控制系统
自从20世纪80年代末以来,离心机已在石油行业得到普遍应用,成为钻井工作(特别是中深井和水平井)中不可缺少的固控设备。离心机分为低速、中速和高速离心机。
低速离心机也称为"重晶石回收型离心机"。对于低密度固相,它的分离点为6~10μm;对于高密度固相,分离点为4~7μm。
中速离心机可分离5~7μum的固相,用于清除钻井液中的有害固相,控制钻井液密度和黏度,这是目前井队使用最多的离心机。
高速离心机分离点为2~5μm,用于清除有害固相,控制钻井液黏度,一般与低速离心机串联使用组成双机系统。在此系统中,低速离心机放在第一级,它分离出的重晶石排回泥浆罐中以回收重晶石,它排出的液体先排人一个缓冲罐中,再用泵把缓冲罐中的液体送入高速离心机中。高速离心机分离出的固体排出罐外,液体回到循环系统中,采用"两机"系统既可以有效清除有害固相,又可以防止大量浪费重晶石。
离心机主要用于回收加重钻井液中的重晶石,及非加重钻井液中的液体或化学药剂,清除0~8μm 左右的细粉砂。目前现场使用的离心机主要有三类。
1.转筒式离心
转筒式离心机的工作原理如图3-13所示。一个带许多筛孔的内筒体在固定的圆筒形外壳内转动,外壳两端装有液力密封,内筒体轴通过密封向外伸出。待处理的钻井液和稀释水(钻井液 ∶水=1∶0.7)从外壳左上方由计量泵输入后,由于内筒旋转的作用,钻井液在内、外筒之间的环形空间转动,在离心力作用下,重晶石和其他大颗粒的固相物质飞向外筒内壁,从一种专门的可调节阻流嘴排出,或由以一定速度运转的底流泵将飞向外筒内壁的重质钻井液从底流管中抽吸出来,予以回收。调节阻流嘴开度或泵速可以调节底流的流量。而轻质钻井液则慢速下沉,经过内筒的筛孔进入内筒体,由空心轴排出。这种分离机处理的钻井液量较大,一般可回收82%~96%的重晶石。
图3-13 转筒式离心机工作示意图
1—钻井液;2—稀释水;3—固定外壳;4—筛筒转子;5—润滑器;6一轻质钻井液;7—重晶石回收;8—驱动轴
2.沉淀式离心机
如图3-14所示,沉淀式离心机的核心部件是由锥形滚筒、输送器和变速器所组成的旋转总成。输送器通过变速器与锥形滚筒相连,二者转速不同。多数变速器的变速比为80∶1,即滚筒每转80圈,输送器转一圈,因此,若滚筒转速为1800r/min,输送器的转速是22.5r/min。其分离原理是∶待处理的加重钻井液用水稀释后,通过空心轴中间的一根固定输入管、输送器上的进浆孔,进入到由锥形滚筒和输送器涡形叶片所形成的分离室,并被加速到与输送器或滚筒大致相同的转速,在滚筒内形成一个液层。调节溢流口的开度可以改变液层厚度。在离心力的作用下,重晶石和大颗粒的固相被甩向滚筒内壁,形成固相层,由螺旋输送器铲掉,并输送到锥形滚筒处的干湿区过渡带,其中大部分液体被挤出,基本上以固相通过滚筒小头的底流口排出,而自由液体和悬浮的细固相则流向滚筒的大头,通过溢流孔排出。
离心机滚筒有圆锥形和圆锥一圆柱形两种,其输送器有双头螺旋和单头螺旋,如图3-15所示。在结构和尺寸一定时,离心机的分离效果与沉降时间、离心力以及进口钻井液量等因素有关。而沉降时间又取决于滚筒的大小、形状及液层厚度。钻井液在离心机中的时间通常是30~50s,时间越长,进口量越小,分离效果越好。
3.水力涡轮式分离机
水力涡轮式分离机结构如图3-16所示。
待处理的钻井液和稀释水经漏斗流入装有若干个筛孔涡轮的涡轮室。当涡轮旋转时,大颗粒的固相携同一部分液体被甩向涡轮室的周壁,并穿过其上的孔眼进入清砂室,聚积到底部;在离心压头的作用下,这一部分浓稠的钻井液再经短管进入旋流器;通过旋流分离,加重剂等从回收出口排出,而轻质钻井液则通过管线返入涡轮室;与此同时,涡轮室内的轻质钻井液,则通过涡轮上的筛孔、上底孔板孔及短管排出。常用离心机技术参数见表3-8、表3-9。
六、除气器
除气器用于除去混入钻井液中的小气泡(气泡直径小于1/16in),确保钻井液有合理的密度,防止混气钻井液被重新循环到井底而导致的井涌或者由于气侵密度偏低而导致不必要的添加重钻井液,造成钻井液密度高于设计密度。总之,除气器能有效地控制钻井作业中钻井液的气侵,安全有效地排除有毒气体或可燃气体。
选择除气器的主要根据是处理钻井液的能力。除气器的处理量指单位时间内除气器处理钻井液的数量,以m³/h计,一般在120~150m³/h。结构不同其除气效率也存在差异,除气效率一般在80%~95%。除气效率随着钻井液黏度的升高而下降。
除气器安装在沉砂罐和第一级旋流器之间,避免了当钻井液中气体含量过多时而导致的离心泵压力降低,甚至影响旋流器的工作。
除气器有真空式、常压式、离心式三种。
真空式除气器是用真空泵吸入钻井液,经薄膜紊流后分离出气体,再由真空泵抽走。这种型号的除气器效果良好,只是体积偏大,比较笨重。
常压式除气器主要部件是离心泵和喷射罐。将气侵钻井液由离心泵送到喷射罐,在罐内形成高速薄层并甩向罐的内壁促使气体破裂、分离、排出。其优点是体积较小,效果良好。
离心式除气器由电动机、抽气机、减速箱等组成。利用离心机分离原理将气体分离出来,它是一种比较新的设备。
-End-